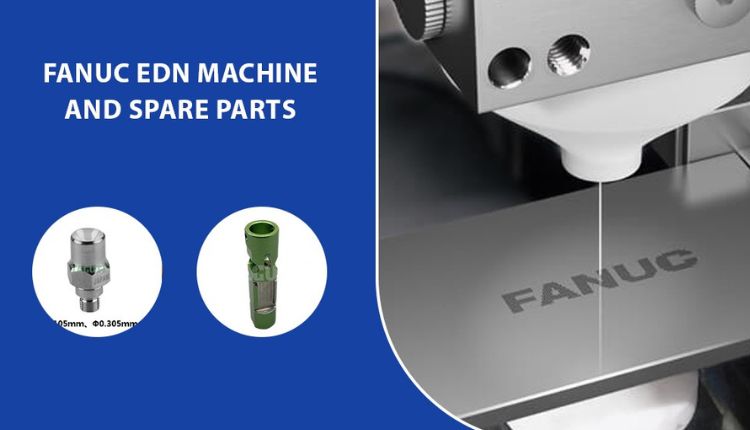
How to manufacture high-precision Fanuc electrodes through precision machining technology
Fanuc EDM Electrodes are key components used in electrical discharge machining (EDM). They are typically made of conductive materials such as copper, copper alloys, silver, molybdenum, etc., and possess excellent electrical conductivity and wear resistance.
The main function of Fanuc EDM Electrodes is to conduct electrical current during the electrical discharge machining process and direct it to the surface of the workpiece to generate the discharge effect. The selection of electrode shape and size is crucial for machining results and efficiency. Different shapes of electrodes can be used for various machining requirements, such as cavity machining, groove machining, wire cutting, etc.
Selecting suitable materials for EDM
Copper (Copper): Copper is one of the most common materials used for Fanuc electrodes. It has excellent electrical and thermal conductivity and corrosion resistance. Copper electrodes are suitable for most applications and are easy to machine and polish.
Molybdenum (Molybdenum): Molybdenum electrodes have excellent high-temperature strength and thermal stability, and are suitable for applications dealing with high-temperature materials and high-energy discharges. .
Molybdenum Copper: The Molybdenum copper alloy combines the advantages of molybdenum and copper. It has high thermal conductivity and thermal stress resistance, and is suitable for high-power discharge and large-size electrodes.
The selection of appropriate Fanuc EDM Electrode materials should take into account specific application requirements, such as electrical conductivity, wear resistance, thermal stability, and corrosion resistance of the materials. Additionally, the electrode size, shape, and machining requirements should also be considered. The optimal material choice will be evaluated based on the specific application and performance needs.
Design and Processing Guidelines
Design and planning: Based on specific electrical discharge machining requirements and workpiece specifications, determine the shape, size, and structure of the electrode. Consider the electrode’s processing performance and service life to carry out a well-thought-out design and planning process.
Manufacturing process: Based on the design requirements of the electrode, employ suitable manufacturing processes. Common manufacturing processes include CNC machining, electrical discharge machining (EDM), electrochemical machining (ECM), and wire cutting, among others.
Precision machining: The manufacturing of electrodes requires high-precision machining processes. Utilizing CNC machine tools or specialized equipment, precise machining is performed to ensure that the electrode’s geometric shape, dimensions, and surface quality meet the required specifications.
Surface treatment of the electrodes
Grinding and Polishing: Using grinding machines, polishing machines, and other equipment, the electrode surface is subjected to grinding and polishing using abrasives and grinding fluids to remove surface roughness and improve smoothness. This process makes the electrode surface smoother, reducing friction and wear.
Pickling and Alkaline Cleaning: By immersing the electrode in acidic or alkaline solutions, it is possible to remove oxides, oils, impurities, and other contaminants from the electrode surface. Acid pickling can be done using acidic solutions such as sulfuric acid or hydrochloric acid, while alkaline cleaning can be done using sodium hydroxide or potassium hydroxide solutions.
Electroplating: Electroplating is a process in which a metal coating is deposited on the surface of the electrode using an electrochemical method. This enhances the electrode’s corrosion resistance and conductivity. Common electroplating methods include chrome plating, nickel plating, and gold plating. Electroplating involves selecting the appropriate electrolyte and current density to control the thickness and quality of the coating.
Chemical treatment: The electrode surface is treated using specific chemical solutions and treatments to alter its chemical properties and surface characteristics. For example, chemical treatments such as oxidation, deoxidation and nitrification can be carried out to enhance the wear resistance, corrosion resistance or electrical conductivity of the electrode.
Coating: Coating materials such as lacquers, polymer coatings etc. are applied to the surface of the electrode to form a protective layer or to change the surface properties. Coating provides the electrode with properties such as wear resistance, corrosion resistance and insulation, as well as adding to the aesthetics of the electrode.
The selection and operation of the above methods needs to be evaluated and determined in relation to the electrode material, application requirements and expected results. When carrying out the surface treatment, care needs to be taken to control the treatment parameters and quality checks to ensure that the resulting surface treatment meets the desired requirements and standards.
Precision inspection of manufactured electrodes
Dimensional measurement: Using measurement tools such as micrometers, calipers, and dial indicators, measure the dimensions and geometric features of the electrode, and compare the actual measurements with the design requirements to identify any deviations.
Shape measurement: Utilizing equipment such as optical projectors, coordinate measuring machines (CMMs), and other devices, inspect and compare the shape of the electrode to ensure its conformity with the design requirements.
Surface roughness measurement: Use a surface roughness meter or a profiler to measure the roughness parameters of the electrode surface, such as Ra, Rz, etc., to ensure that the surface finish meets the requirements.
Sealing inspection: For electrodes that require sealing, a sealing test can be performed using equipment such as a leak tester or immersion tester to assess the sealing performance of the electrode.
Conductivity testing: For electrodes that need to have good conductivity, equipment such as conductivity testers or resistance meters can be used to measure the conductivity of the electrodes to ensure they meet the requirements.
Corrosion resistance testing: Depending on the required corrosion resistance of the electrode, corresponding corrosion tests such as immersion tests and salt spray tests can be carried out to assess the performance of the electrode under specific corrosive media.
The above are common methods for electrode precision inspection. The specific inspection methods and equipment selection should be evaluated and determined based on the characteristics of the electrode, manufacturing requirements, and application environment. When performing precision inspections, it is important to ensure the accuracy and reliability of the inspection equipment and follow the corresponding standards and specifications for operation.
Maintenance
Cleaning and maintenance: Regularly clean the surface of the electrode to remove any dirt or residue. You can use specialized cleaners or solvents, along with a soft cloth or brush, to gently wipe the surface.
Rust prevention: For metal electrodes, it is important to prevent rust formation. You can use rust inhibitors or coatings to provide protection and avoid contact between the electrode and moisture or corrosive media.
Regular inspection: Regularly inspect the electrode for wear, surface condition, and dimensional accuracy. If any abnormalities or significant wear are detected, promptly repair or replace the electrode to ensure machining quality and accuracy.
Proper lubrication: For electrode components that require lubrication, such as guide rails and sliders, proper lubricants can be used for maintenance to ensure smooth and stable electrode movement.
Storage precautions: Store the electrodes correctly to avoid moisture, heat or pressure. The electrodes should be placed in a dry, clean environment and avoid collision with other objects or being crushed.
Adjustment of usage: According to the usage of the electrode and the processing requirements, adjust the usage parameters and the processing method at the right time to reduce the wear and damage of the electrode.
Regular maintenance: Depending on the frequency of use and working environment of the electrodes, a regular maintenance plan is drawn up, including cleaning, lubrication, inspection and adjustment to ensure the normal operation and long life of the electrodes.